Background
A leading automotive manufacturer was faced with a series of interrelated data challenges:
- Lack of data Standards: There is a large number of software across a vehicle programme, from vehicle and facility design, through robotics, tooling, and simulation, to manpower planning. Uncontrolled data conversion is time consuming and can introduce errors with multiple sources of truths.
- Lack of Process Standards: Efforts to standardize manufacturing processes through a series Bill of Processs (BoP) were ineffective, as teams relied on Excel and PDF documentation. This hindered real progress in improving consistencies and compliance.
- Siloed Operations: A cultural divide between design and manufacturing teams meant that designs were often “thrown over the fence,” reinforcing a siloed approach that stifled collaboration and innovation.
- Data Discrepancies: Virtual-physical misalignment created data veracity gab throughout the lifecycle of a vehicle programme. Shop-floor decisions were frequently not fed back into the digital model, and data fall out of sync with reality. This misalignment led to a lack of trust in the data, resulting in further ad-hoc decisions that worsened the problem.
The company had secured funding to invest in virtual manufacturing and is seeking a Digital Twin roadmap as a first step to resolve the data challenges.
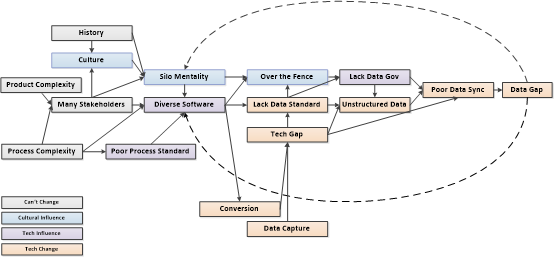
Outcome
After consultation and exploration with their multi-disciplinary teams , we developed a Digital Twin Roadmap to help the organization achieve Level 3 Digital Twin Maturity.
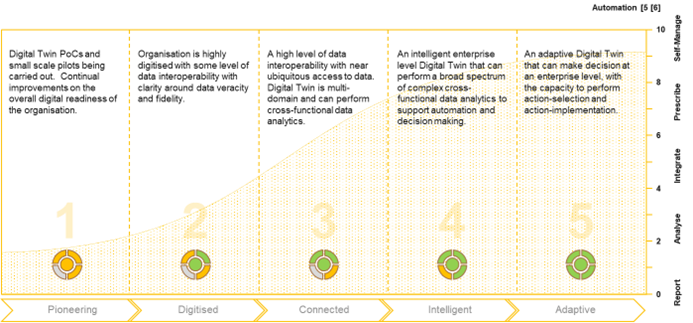
The roadmap consists of six tranches of activities 1) Data Consumption; 2) Data Infrastructure; 3) Data Interface; 4) Data Capture; and 5) Data Analytics, with four milestones across four project phases.
- Phase 1 prioritizes UX/UI design and visual analytics development with an emphasis on user engagement with digital models and assets.
- Phase 2 establishes a Sandbox Digital Twin Environment (DTE) to consolidate data modelling and data preparation standards, with initial integration of Discrete Event Simulations (DES).
- Phase 3 deploys a functional DTE with real-time data connectivity with Manufacturing Execution Systems (MES). This phase also develops a VRAR content development environment to allow for the creation and integration of Digital Twin assets. The objective of phase 3 is to integrate the DTE with a pilot manufacturing facility.
- Phase 4 aims to extend and scale the DTE’s capability by enhancing the user interface, data validation and sychronisation, and building a full content development pipeline.
This roadmap laid the foundation to redefine the company’s data infrastructure to integrate with future manufacturing capabilities.